Objectives
Analog playback is a challenging environment that requires unique solutions to address external and internal vibration sources. The reproduction chain from the original musical event to playback undergoes numerous degradations to arrive in the form of a vinyl disc.
From that point on the mechanism used to play the vinyl disc will introduce further intermodal vibrations which change the sound subjectively and objectively.
For example, floor-borne and structure-borne vibration can cause an intermodulation of low frequency modes into the stylus tip and cantilever suspension resulting in unwanted movement and signal intermodulation.
Airborne vibration from loudspeakers can also affect a turntable arm and cartridge system.
With the internal mechanical environment of a turntable, the motor, bearing and platter will generate noise and vibration as well as lower frequency modes from platter wobble and precession (spinning top analogy). Finally, the stylus mechanically vibrates the very medium it traces to create a vibration source directly at the “groove reading” interface.
This unwanted energy can be heard as distortion, smear, added harmonics, channel imbalance and can often obscure the micro-details within the recording as well as add a colouration to the music.
Our objective is to mitigate as much as possible of these resonance energies so that playback can be as accurate and pure as possible, thus bringing the listener closer to the musical event.
The Helix Platform
To address each of these subjective and objective intermodal elements the Helix platform is based on a modular series of “design blocks”. These sub-systems are integrated and interfaced with each other to provide a solution stack.
Each layer or sub-system of the architecture is designed to address the inherent problems in analogue information retrieval which are affecting that layer prior to “hand-over” to the next dependent subsystem in the solution stack. Analogous to a mechanical crossover where frequencies are filtered out to preserve the best operational environment for each element.
At the top of any analogue “stack” is the tonearm and then the cartridge/stylus. These two sub-systems form their own combination of matching parameters and are left to the listener’s preferences.
The Helix platform is very accepting of a wide range of commercially available tonearms and cartridges. The underlying principle is to provide a quiet and structurally effective isolation and damping system to allow the tonearm and cartridge to reach their full potential. This is where the challenges become complex.
There are 8 main sub-systems within the Helix platform:
Solution Stack | Sub-System |
---|---|
Foundational Layer | 1. Integrated MinusK Isolation Mechanism |
Intermediate Layer | 2. Tuned Damping Systems 3. Pre-Stress Accumulation Release System 4. Bearing |
Upper Layer | 5. Floating Advanced Composite Armboard 6. Platter 7. Mk3 Clamp 8. Motion Control |
1. Foundational Layer
Integrated MinusK Isolation Mechanism
The foundation of the Helix solution stack commences with a MinusK – Negative Stiffness mechanism (using a customised version of BM platform refer www.minusk.com) to address low frequency vibrations found in most domestic and professional environments. This system provides superior passive noise and vibration isolation for vinyl playback due to its unique ability to provide true isolation from 0.5hz upwards to 100hz with an ability to tune the system for specialised needs.
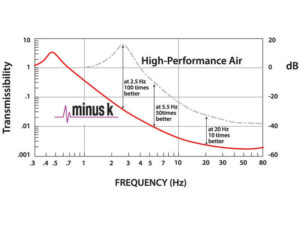
Placing a turntable on a MinusK isolation platform is helpful but not ideal as the energy between the two devices needs to be managed. For this reason, the MinusK mechanism used by Dohmann Audio is a custom design version that facilitates total integration into the turntable sub-chassis.
Compared to high performance air bladder suspensions and active systems, the passive MinusK low natural frequency provides critical isolation starting at 0.7hz to deliver over 100 times better performance at 2.5hz where a lot of environmental noise is active. The system also doesn’t shoot into active overdrive or shunting whilst under movement which is difficult to ameliorate in active solutions.
In critical optical imaging systems such as atomic force or electron microscopes this can be measured on the clarity of the image under test. In analog systems this can be heard in a lower noise floor and cleaner sonic imaging and fine detail retrieval. The MinusK system is designed to work well in the low bass area to remove subjective vibrational signatures from affecting the stylus. We hear these as bass smearing, bass definition and delineation.
2. Intermediate Layer
The turntable now needs to deal with resonances within a higher frequency range. In addition, to further enhance the listening experience, vibration signatures emanating from the bearing and motor systems require solutions to reduce their impact on the sonic performance of the turntable.
The Helix platform uses a series of stacked plates which provide a high damping factor to each “noise” generating element. With the specific low frequency high compliance suspension provided by the Minusk the motor should be mounted on the same plane as the bearing system to reduce “yawing” in the suspension system (a common problem in suspended turntable designs where motors are mounted external to the suspension).
Each of the separated plates mounts the motor and bearing on different insulated and damped layers vertically but locks these geometrically in the horizontal plane to ensure accurate operation in groove. Each plate is separately tuned by highly specialised analysis and localised stress deformation to move any vibrations away from critical mounting areas.
Tuned Damping Systems
One of the major influences in the sound reproduction of vinyl play back is mechanical vibration. After all, turntables are mechanical devices. What if a “mechanical crossover” concept could be extended to create a smooth continuous pathway to channel vibrations away from critical areas on a turntable?
The Helix platforms use our proprietary TDS solution which forms a semi-active damping system to further lower the noise floor of the overall system. This technology uses a pre-stress accumulation release (PAR) strategy to mitigate vibrations inside the chassis caused by motor bearing and platter bearing noise. This technology creates a path of least resistance for these vibrations, channels them away from the critical signal path zones and dissipates the energy.
The primary source for energy dissipation is the material damping of higher frequency vibrations. Whilst frictional dissipation contributes to the system balance using constrained layer plates each plate has been designed using the latest Finite Element Analysis (FEA) and Finite Element Modelling (FEM) methods in advanced software (COMSOL).
Energy dissipation contributions at the time instant of node activation, amount to around 80% for material damping and 20% for frictional dissipation. There is additional dissipation not associated with any physical process (derived using Hilber-Hughes-Taylor calculations of motion).
Established engineering principles include using Chladni Plate Analysis which form the underlying scientific approach to vibration measurement. Using localised stress deformation techniques the behavior of the plate modes can be altered to address problem areas found in turntable designs. A designer can effectively move vibrations at specific frequencies away from critical areas to help lower the noise profile the stylus may encounter in non-optimised designs.
Pre-Stress Accumulation Release
The turntable is equipped with a device that constrains the relative slip between layers of plates. The strain accumulated in the structure locally is released as it occurs which results in conversion of a part of the strain energy to the kinetic energy of local, higher frequency vibrations. These higher frequency vibrations are then sunk into heavy damping materials which absorb and convert these to heat.
The equilibrium is restored rapidly to allow the structure to return to the initial state by means of a gradual release of the pre-stress accompanied by the frictional dissipation in the contact surfaces. This architecture is used as a Mechanical Crossover to selectively reduce each band of frequencies.
The MinusK NSM system absorbs and isolates low frequency vibrations up to 100Hz and the Mechanical Crossover then uses the complete constrained layer plates to absorb mid-band vibrations. Higher frequency artefacts are then focused and dissipated in the PAR system.
From this method we learn the shape and weight of the components influence acoustic behaviour under vibration. Therefore, the selection of materials and the suspension elements used determine the crossover frequency and effectiveness!
By extending the mechanical crossover concept to the Helix platforms, physical zones can be defined on the infrastructure that focused vibrations away from key areas (platter, bearing, motor, tonearms, floor modes), establishing a smooth continuous pathway to channel vibrations away from critical areas on the turntable.
The Helix platforms have been designed to reject low frequency vibrations coming up from the floor by using the MinusK NSM isolation system and drive higher order vibrations generated through motor noise away from the bearing and platter via a complex coupling to the chassis. For these higher order vibrations local isolation, absorbing, redirecting and suppression technologies are employed including semi-active decoupling from motor vibration.
Helix turntables have been designed to operate flawlessly in non-ideal environments suffering from floor-borne vibrations such as older houses with wooden floors, upper floors, attics and any external vibrations which are carried through buildings – even those made from concrete steel and brick.
The Bearing
The hydrodynamic bearing was optimised by use of fluid film calculations and advanced spindle error measurement metrology tools. These include working with the thickness of lubrication film and the diameter of the bearing to ensure stable operation with much tighter tolerances. This means the bearing is centered at very low rotation speeds, which ensures low TIR (Total Indicated Runout including out of center, eccentric and precession toppling errors).
The hydrodynamic bearing is made from precision ground steel shaft and post with DLC (Diamond Like Coating) amorphous thin film on high pressure areas for smooth operation.
The low height bearing design also maintains an important relationship with the suspension system to reduce precession effects (toppling modes) from a heavy platter wobbling high up in an over tall design. The Helix platform is therefore highly integrated with the suspension system and not an aftermarket addition. It places the center of mass at the correct plane of isolation.
3. Upper layer
The Floating Advanced Composite Armboard
The armboard is a specialised area of vibration isolation and critical damping inside the Helix platform. The Helix Armboard technology uses carbon fiber, high-damping alloys, specialised high energy absorbing polymers and hardened stainless steel plates for stiffness and critical damping in a constrained layer multiple material “sandwich”.
This sandwich mounts onto a magnetically damped mounting rail which is further decoupled from the chassis and bearing and motor. It’s a passive system, but the magnetic dampers provide real-time semi-active vibration suppression. It doesn’t overshoot or go into self-resonance which can occur in servo based piezo or active systems.
Effective mitigation of such vibration further extends the performance of any tonearm mounted on the armboard. This semi-active magnetic technology attenuates the last vestiges of noise generated by vibrating structures. The system does not require power or any servo feedback and has a larger restoring force than the physical drag caused by a stylus in the groove.
This geometrically locks the system into the chassis whilst it isolates the armboard from motor and bearing noise. This innovation was pioneered in the earliest Dohmann turntable designs. The system is in effect an adaptive shock-absorber and control for energy dissipation in a flexible floating plate structure.
The Platter
Our platter technology uses high damping metals and polymer constrained layer construction and a very special mat material for record interface.
There are three main layers in the platter assembly. The lowest layer is the sub-platter for belt drive which is inertially matched to the drive and uses a proprietary powder and resin matrix to damp belt noise from the separated upper platter system designed for sonics.
We avoid running metal under the cartridge assemblies to avoid eddy current (Lorentz force) effects on the cartridge magnet system. Our non-magnetic polymers are also not interrupted by metal slugs or weights. This avoids passing eddy current inducing metals under the stylus damper assembly.
The Spindle is separated into the upper platter and doesn’t directly contact the thrust pad in the bearing. This is to further reduce bearing noise from entering the record surface.
The Mk3 Clamp
The clamp is designed to address ‘internally’ generated noise from the interaction between the stylus and the record grooves. The clamp attenuates these “self-chatter” resonances using a large mating (damping) contact surface area compared to traditional point loaded designs.
Metallurgy was specifically chosen for transmission purposes with internal chambers used for the critical damping materials. One material cannot provide the broad frequency spectrum needed – it needs to be a carefully selected group of materials.
We measured resonances through the spindle (stem) which originate in the bearing. These frequencies need to be addressed by different tuned materials and the upper section of the clamp has its own purpose-designed chambers to allow addition of specialized polymers.
A third constrained layer ring system is used to separate the upper and lower chambers which under clamping pressure creates a dissipation plate (designed using Finite Element Method) that is shaped carefully to provide an optimum boundary interface.
The cumulative outcome from addressing these challenges is a discernible improvement in clarity, resolution, focus, dynamic contrasts and tonality within the sonic presentation of a turntable.
Motion Control
The Helix platform uses a traditional belt drive approach for the sonic attributes a well-designed belt drive system can deliver.
Our motion control uses a 3-phase motor (DC Brushless) driven by a DSP engine to deliver 3 sine waves precisely to minutely controlled to smooth the operation of the drive to exceptional levels of performance. The servo control is operating at 100khz which is well out of the audio spectrum and allows for smoothing and balancing of the rotation of the platter.
The motor spins at 330 rpm to deliver 33 rpm at the platter using a 10:1 ratio to blend off any servo errors which would affect a direct drive using a similar high-performance cog-less motor if driving a spindle directly. In listening tests, the belt drive system was preferred when evaluating music.
Sonic signatures of drives are very audible to experienced listeners and adding brightness or harshness to the music signal with rapid servo correction can be avoided using the step-down ratio of a smaller pulley driving a larger sub platter. Inertial balancing is also very important to allow the motor and pulley to work effectively with the belt tension / material to further smooth the platter operation.
Our belt drive design places the motor and the bearing on the same plane. This is a reason our belt drive topology is often compared favourably with rim drive and direct drive designs in terms of stability and drive authority for dynamics and crescendos.
Dohmann Helix turntables have often been chosen for major transcription / archival applications. Culturally critical archival LP retrieval project managers such as Stanford University USA have chosen the Helix Platform as their reference to help capture and restore rare vintage recordings. The fine speed control the Helix system provides is carefully matched to each original recording up to 100RPM operation.
Visualisation, R&D and the Human Ear
The measurement and visualisation techniques that are used which enable the Dohmann engineering team to ‘see’ these vibrations in real life, especially how they move and where they ‘collect’ on a chassis under real life operating conditions are highly advanced and span many engineering disciplines. Dohmann Audio have invested significantly in precision measuring equipment that enable unprecedented data collection around resonance mapping and energy movement within mechanical systems. Without this data, the development of the Dohmann suite of technologies would not be possible.
However, we don’t sacrifice the music, tonality, emotional engagement at the altar of “numbers”. We rely on a dedicated experienced listening panel to review and authorise all our design and build prior to market release to ensure our reputation for building some of the finest music playing systems available is maintained. New products and technologies are ‘blind-tested’ through our listening panel where the ultimate aim of a music system is put to the test – to connect the listener emotionally to the artistry, the beauty, the message and intention of the artist.